Типы планирования производства
В зависимости от типа производства существуют различные типы планирования производства.
В функциональной компоновке производственные ресурсы группируются в соответствии с выполняемой задачей. Конкретные отделы выделяются для различных видов услуг (отдел двигателей, кузовной отдел и т.д.). Его можно использовать в мелкосерийном производстве.
При таком типе компоновки возникают проблемы с минимизацией работы по переносу.
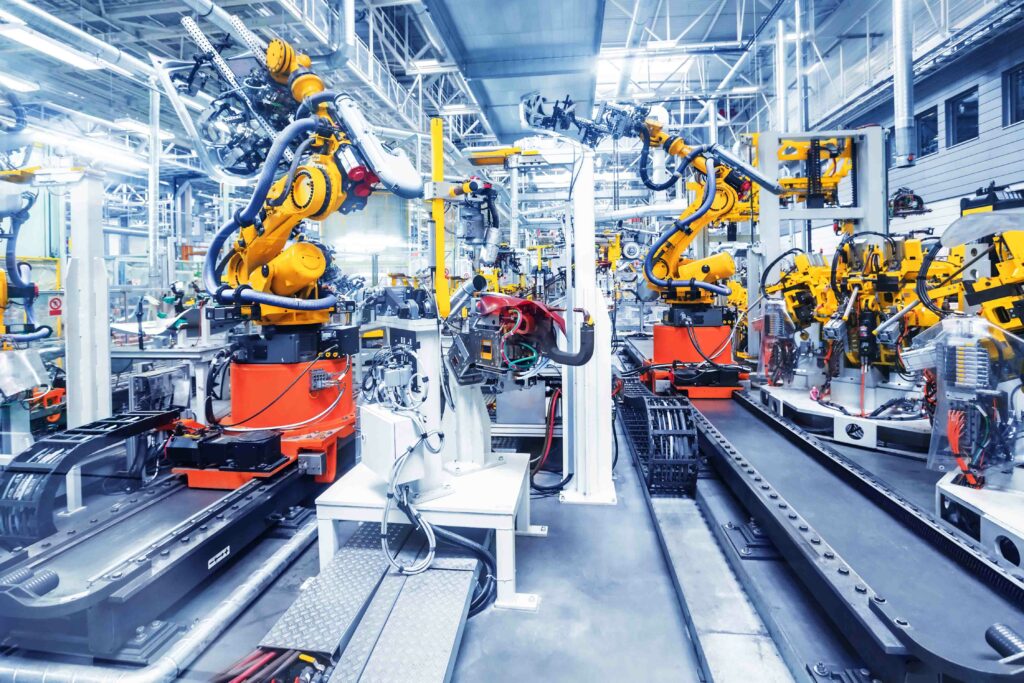
При устройстве с фиксированным положением производимый продукт фиксируется, а производственные ресурсы предоставляются по мере необходимости. Это положение используется в нескольких работах. Такая договоренность является временной и остается в силе до завершения проекта.
Массовое производство характеризуется линейной или поточной схемой, при которой каждый произведенный продукт подвергается одним и тем же процессам обработки. Таким образом, поточное производство характеризуется разделением производственного процесса на отдельные, относительно короткие операции, выполняемые на специально оборудованных, последовательно расположенных рабочих местах – поточных линиях.
Поточная линия – это набор устройств, которые соединены друг с другом и работают в соответствии с заданным ритмом технологического процесса. Рабочие места расположены в соответствии с последовательностью технологического процесса.
Непрерывность производственного процесса обеспечивает высокий уровень специализации и создает условия для использования автоматического оборудования.
Основная проблема заключается в правильном распределении нагрузки на рабочие станции с целью устранения перегрузок.
Конструкция потока типична для химической, автомобильной, пищевой и т.д. промышленности.
Проводится различие между системой “выталкивания” и системой “вытягивания” для продукта, который был запущен в производство.
Наиболее часто используется система вытягивания. Предполагается, что производство продукта начинается на одном конце производственной линии, проходит ряд технологических операций и заканчивается обработкой на другом конце производственной цепочки. После обработки на сайте продукт “перемещается” на следующий сайт, независимо от того, готов он принять продукт для обработки или нет. Каждый регион имеет свой собственный производственный план. Однако невозможно создать “жесткий” производственный процесс со всеми заранее точно рассчитанными параметрами. Поэтому компании всегда должны иметь определенный запас продукции, что повышает гибкость системы. В то же время известно, что увеличение запасов связано с мертвым капиталом, требующим значительных затрат на хранение и техническое обслуживание.
Система с
Рисунок 2.8: система с “выталкивателями”.
Поточная производственная система с “наполнением” продуктов (рис. 2.9) помогает сократить производственные запасы, одновременно повышая гибкость производства. Эта система предполагает поставку продукции с предыдущей производственной площадки по мере необходимости. Впервые он был испытан в 1972 году в автомобильной промышленности Toyota.
Система с
Рисунок 2.9: система “вытягивания”.
Автор этой системы использовал принцип “последнего звена”, используемый в супермаркетах для промышленного производства. В супермаркетах покупатель является источником информации о требуемом количестве, ассортименте и т.д. Стимулом для всей системы является спрос, который определяется покупателем. Аналогично, на промышленных предприятиях чертеж есть только у готовой сборочной линии, поэтому информация о необходимости изготовления определенных деталей доходит до предыдущих пунктов через специальные карточки ASD-BAN (иногда в литературе используется термин KAM-BAN).
Существует два типа карт:
- карты выбора,
- карточки заказов на производство.
В карточке выбора указывается количество деталей, которые должны быть получены в предыдущем разделе обработки.
В карточке производственного заказа указывается количество деталей, которые должны быть изготовлены в предыдущей обрабатываемой детали.
В складском помещении детали загружаются в вилочный погрузчик в количестве, указанном в карточках выбора. При этом удаляются прикрепленные к коробкам карточки заказов, в которых указан заказ на производство новых деталей в строго определенном количестве.
Пакетный план создается каждый день. Это делает систему гибкой. Ни одно место не может быть перемещено без карточек. Обычно система ASD-BAN сочетается с системой контроля качества. Система CAN-BAN не требует полной компьютеризации производства, но предполагает высокую дисциплину при доставке и высокую ответственность персонала, что ограничивает ее внедрение в разных странах.